Agar Plate Desiccation: Cherwell's Insights Feature in Cleanroom Technology
Written By: Martin Sketchley |
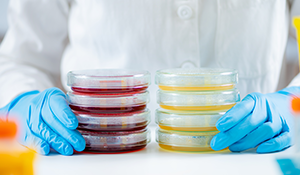
Desiccation of agar is a significant challenge in pharmaceutical environmental monitoring (EM). It affects the accuracy of detecting microbial contamination in cleanrooms and other controlled environments.
Cherwell, AnalytiChem's UK production facility and birthplace of the Redipor brand, recently explored this issue in an article published in the March edition of Cleanroom Technology. The article highlighted key causes and consequences of agar desiccation and also proposed solutions to the problem.
Understanding the Impact of Desiccation
Settle plates play a crucial role in monitoring airborne microbial contamination, particularly in sterile manufacturing environments. But exposure to high airflow, temperature fluctuations, and low humidity levels, can cause agar plates to dry out.
Desiccation of agar can lead to false-negative results due to impaired microbial recovery, which ultimately impacts contamination control strategies and regulatory compliance.
Our explainer animation highlights the causes of desiccation, and potential solutions.
Key Causes of Agar Desiccation
Cherwell's article identifies several factors that contribute to desiccation:
- High Airflow Exposure: Unidirectional airflow from HEPA filters and laminar flow cabinets accelerates moisture loss.
- Temperature and Humidity Fluctuations: Cleanroom conditions typically maintain low humidity (30–40% RH), which exacerbates evaporation.
- Gamma Irradiation Effects: While necessary for sterility, excessive irradiation can alter media properties, increasing desiccation risk.
- Variability in Media Composition: Different formulations may have varying resistance to desiccation, influenced by factors such as fill volume and neutralizer content.
Practical Strategies for Mitigation
To prevent desiccation and improve the reliability of EM data, Cherwell's article outlines several best practices:
- Minimize airflow exposure: Avoid placing plates directly under unidirectional airflow and use shielding methods where possible.
- Optimise storage and handling: Maintain controlled temperature and humidity conditions throughout storage and use.
- Refine incubation practices: Adjust fan speeds in incubators and position plates strategically to reduce dehydration.
- Select the right media: Work with your supplier to identify formulations with higher moisture retention properties and reduced susceptibility to cracking.
- Regularly inspect and validate plates: Implement routine checks to detect desiccation early, and assess its impact on microbial recovery.
Enhancing Contamination Control Strategies
By understanding and addressing the causes of agar desiccation, pharmaceutical manufacturers can ensure more reliable environmental monitoring results. For a deeper dive into this topic, read the full article in Cleanroom Technology's March issue.
With our Redipor range, AnalytiChem continues to support the industry with high-quality prepared media solutions designed to withstand the challenges of cleanroom environments, such as desiccation of agar. These include fill volumes with greater ability to withstand the impact of high airflow environments, and custom formulations designed to meet your specific requirements.
To learn more about our Redipor range, custom formulations and bespoke packaging solutions, contact our team today.